Dive Deeper Into Our
Technology
Aerodynamic and
Mechanical Design
Drones require lightweight, strong, and energy-efficient designs for nearly all their applications. Our extensive experience in aerodynamics and CFD, combined with our unique expertise in composite materials, results in drone platforms that are not only light and structurally robust but excel in flight performance, wind stability, and durability for any use case. See if our platforms can help you.
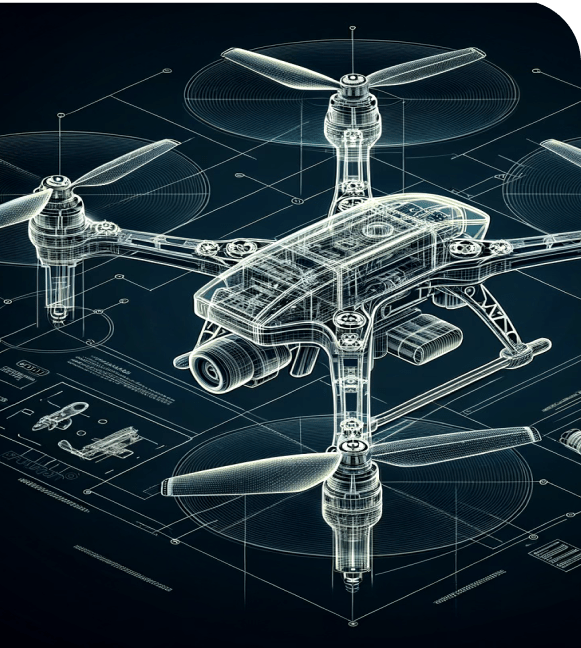
Algorithm
Flight control and system control algorithms require precision and stability to support both autonomous and piloted operations. They need to provide accurate navigation through adaptive and rapid feedback loops for effective mission control across all applications. The Aerora Active Disturbance Rejection Control (ADRC) achieves this by mitigating errors inherent in the Proportional Integral Derivative (PID) algorithm and by not solely relying on mathematical models of its environment. Instead, it quickly observes disturbances and errors and adapts accordingly. Our solutions have been proven effective in multirotor, fixed-wing, and tilt-rotor flight platforms and have been successfully integrated into our gimbal systems. Speed your platform development times and use these algorithms.
Battery
We create tailored, high-performance battery packs, ideal for a wide range of applications from energy-dense industrial drones to lightweight FPV setups. Equipped with state-of-the-art testing facilities, we conduct rigorous assessments at both cell and pack levels to guarantee superior quality. Our tests include capacity, cycle life, discharge capability, and extensive thermal assessments in controlled environments. Leveraging strong partnerships with various cell vendors, we then provide an extensive selection of battery types, including LiPo, Li-ion, LiFePO4, 18650, and pouch-style cells, tailored specifically to your needs—from design and cell sourcing to mechanical integration and mass production. Ensuring your product reaches the market quickly and efficiently.
Electronics Design
Our hardware expertise ranges from flight controllers and Battery Management Systems (BMS) to advanced sensors and image modules. We conduct risk assessments and implement robust safety protocols, including redundant backups for crucial flight controllers and sensors for maximum reliability. Our innovative electronic speed controllers feature both Brushless Direct Current (BLDC) and Field-Orientated Control (FOC) technologies, designed to meet a wide range of operational needs from low to high power setups, thus enhancing efficiency and reducing costs. Our diverse design experience across industry-leading platforms like Intel, Rockchip, Qualcomm, Hisilicon, Nvidia, Amba, TI, and ST, coupled with our approach to signal integrity, thermal management, and power optimization, allows us to deliver high-performance hardware solutions that are both stable and scalable. Committed to excellence, we utilize real-time simulation for high-speed PCB designs with the highest standards of accuracy. Let’s get started.
Electronic Speed Controller (ESC)
Our patent pending Field Orientated Control (FOC) algorithms for sensorless solutions greatly reduce cost, increase reliability, and lowers noise for your drone. Implemented with an extremely high bandwidth observation and signal recovery we have optimized for a rate of 60k calculations per second. The results are motor control with 50% higher RPM than industry standard limits. In an innovative “worry-free” mode our FOC electric speed controller can switch from 1000 RPM to reverse 1000 RPM within 200 ms which is essential for emergency conditions.
Embedded Software
Engineers from diverse industries such as robotics, telecommunications, smart home, and security, with years of expertise in embedded platforms like Qualcomm, MTK, Rockchip, Amba, Hisilicon, and Nuvoton. We excel in full-system customization on Android and Linux platforms, covering everything from BSP and frameworks to app development. We design sophisticated device software systems specifically for various UAV architectures that include onboard image acquisition, visual computing systems, and intelligent portable ground station systems. Additionally, we enhance SoC video streaming and visual computing capabilities to ensure low-latency image transmission and high-frame-rate computing.
Gimbal
We redefine gimbal stabilization with unmatched precision of +/-0.005° through innovative control and FOC motor drive algorithms, setting a new industry benchmark. Our gimbals, when equipped with a 30x optical zoom utilize brushless motors crafted from special magnetic steel to drastically reduce cogging effects. Enhanced with high-precision magnetic encoders and advanced calibration algorithms, our system effectively compensates for production variances, ensuring flawless image stabilization. The rapid 100-microsecond response time of our FOC algorithm and our Anti-Disturbance Resilient Control (AAFC) consistently deliver real-time, precise attitude adjustments, leading the field in dynamic control.
Motor Design
Our motor design expertise spans from the nimble 08 series to robust 95 series motors, and innovative gimbal motors up to 3 kg, crafted through advanced electromagnetic and thermal analyses to ensure top-tier reliability and performance. By shunning conventional trial-and-error methods, we calculate precise motor parameters tailored to specific requirements, optimizing weight and power efficiency. Our unique use of sinusoidal waveform technology in magnet motors enhances control accuracy, setting our lightweight yet durable motors apart in the industry. Through integrated empirical and cutting-edge simulation methods, we accelerate design perfection, significantly reducing prototype cycles and costs.
Propeller
Our advanced rotor design capabilities set us apart, consistently outperforming market standards through a sophisticated, proven process. Starting with in-depth client requirements on size, endurance, and cost, we use blade element and momentum theories combined with a rich database of past projects to meticulously craft airfoil shapes and dimensions. This initial design undergoes rigorous optimization via 2D cross-sectional analysis and 3D CFD simulations, enhancing aerodynamic efficiency from root to tip. Our process culminates in prototype validation, leveraging both empirical data and theoretical insights to refine performance, typically halving development time and cost while accelerating the production of superior rotors.
GET IN TOUCH
Headquartered in Santa Clara, CA., our team is ready to assist you.